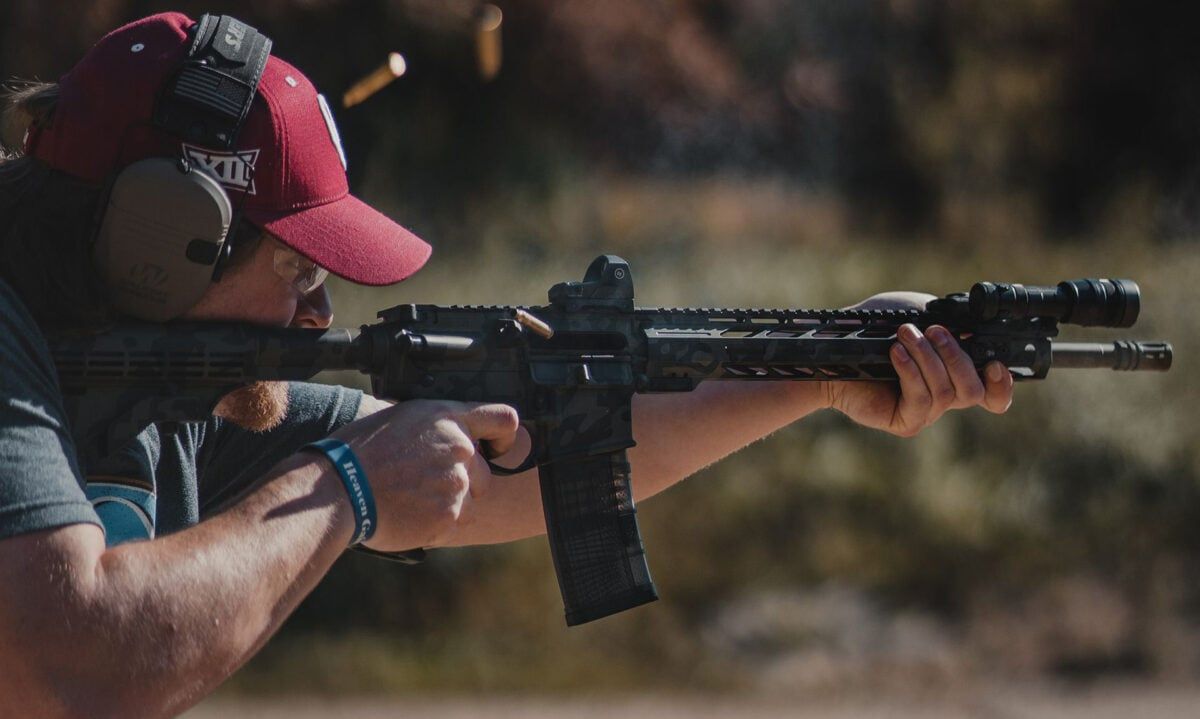
We recently sat down with Bob Faxon of Faxon Firearms for a wide-ranging interview covering his company’s history, lessons learned on AR barrel making, expanding his product line, and his company’s recent work on barrels for the 8.6 Blackout.
Q: Bob, thanks for sitting with us. Let’s start with some background. How did Faxon Firearms as a company start?
Bob Faxon, Faxon Firearms – We started in Cincinnati in 1978. Our older brother, David, actually started a company called Faxon Automotive and Machining. Barry, my older brother, and I helped him. Barry was 15, I was 13, and Dave was 19. Sadly, our older brother Dave was electrocuted in 1984, off-site, in an industrial accident. Barry and I then took over the machining business at 19 and 21 years old. It was a bad thing.
The building we took over was 4,500 square feet…it was during the Jimmy Carter days, and there were issues with interest rates, the economy, etc. It was not a great economic time, and it was challenging from a business perspective. That said, We kept working on it every day. I would note that our mom and dad had actually helped David start the business, and until they both passed, they continued to be instrumental in the company. They were incredible supports and backbones for us, allowing Barry and me to focus on the business.
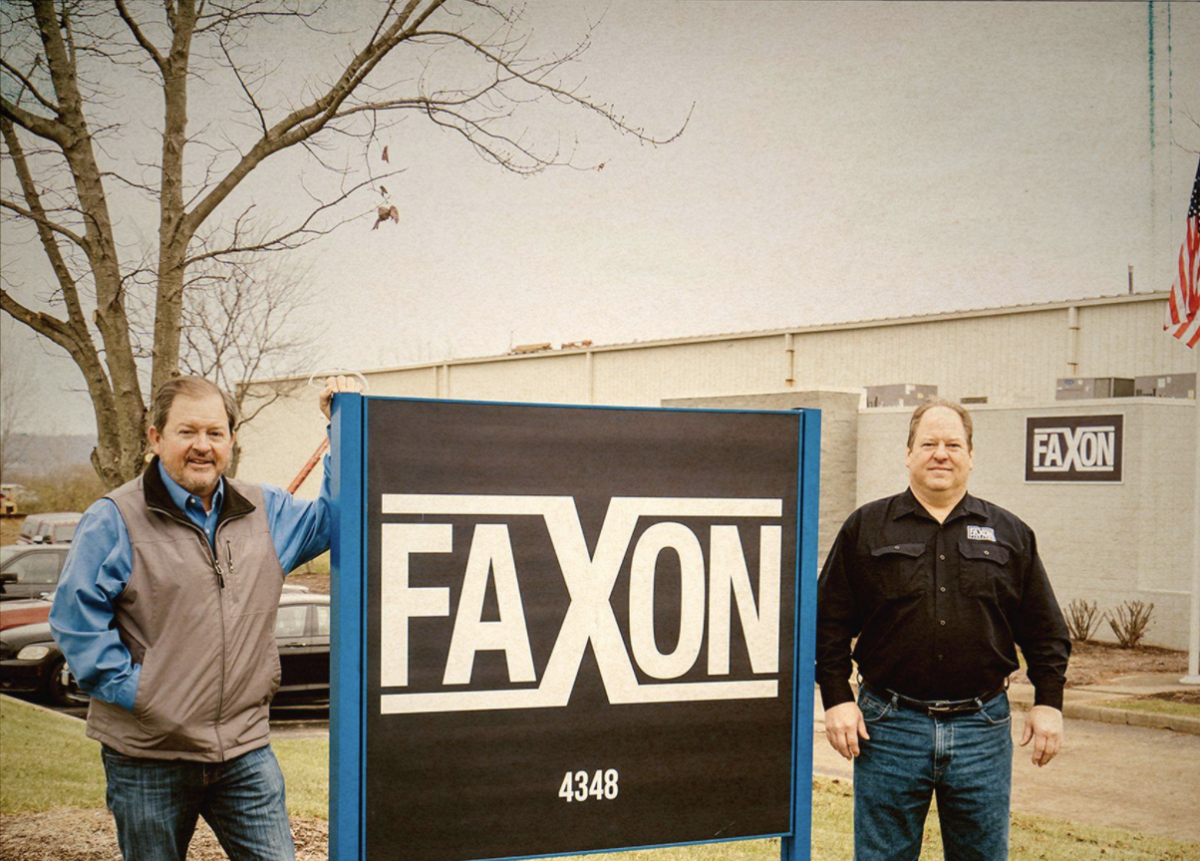
Q: Where did the idea to move into firearm parts come from? Due to the precise nature of machining, I can see where it would be a good fit.
Bob Faxon, Faxon Firearms – When the business was bought in 1978, it was called Weichold Arms, and they made muzzleloaders back then. We didn’t know that. Of course, I was 13, and my oldest brother was 19. They bought the building, and inside it was one twin-spindle Bausch gundrill. My dad told the gentleman who owned the building, Bill Weichold, that we’d buy the building if he left the machine. He agreed and left both the gundrill machine and a small box of 3×5 index cards that was a customer list. My dad handed that small brown metal box to my brother and said “here you go, if the car business gets slow, you can drill some holes.” (laughs)
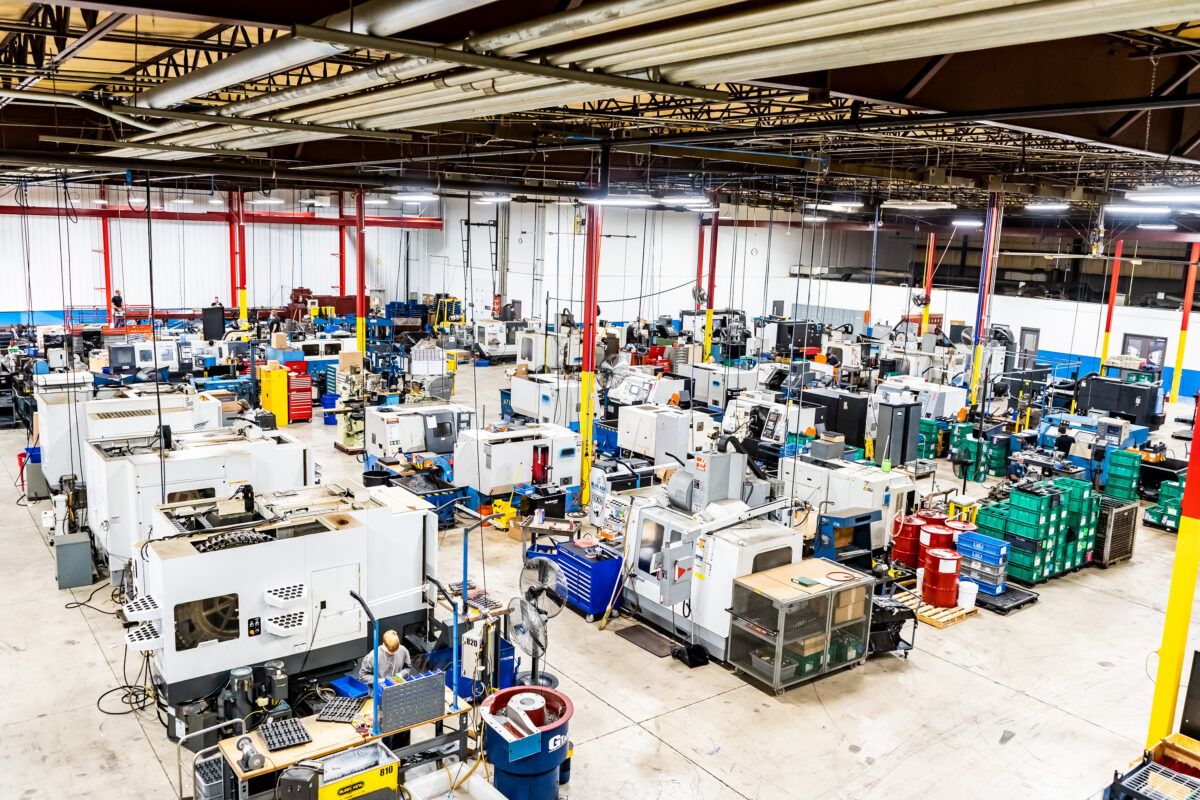
In the years since, so much has changed. In regards to machining, the evolution of machining – capability, expectations, technology, equipment – has been dramatically changing in the last 2 to 5 to 10 years, over the 40-plus years prior. It’s changed so much. The machining mentality has also been something of a precise nature.
You might think of an old tool and die maker, but things have evolved dramatically. Much of the individual skill with manual equipment has been replaced with technology and machine capabilities. However, it is still imperative that the person running the machine has an incredible sense of precision at the end of the day.
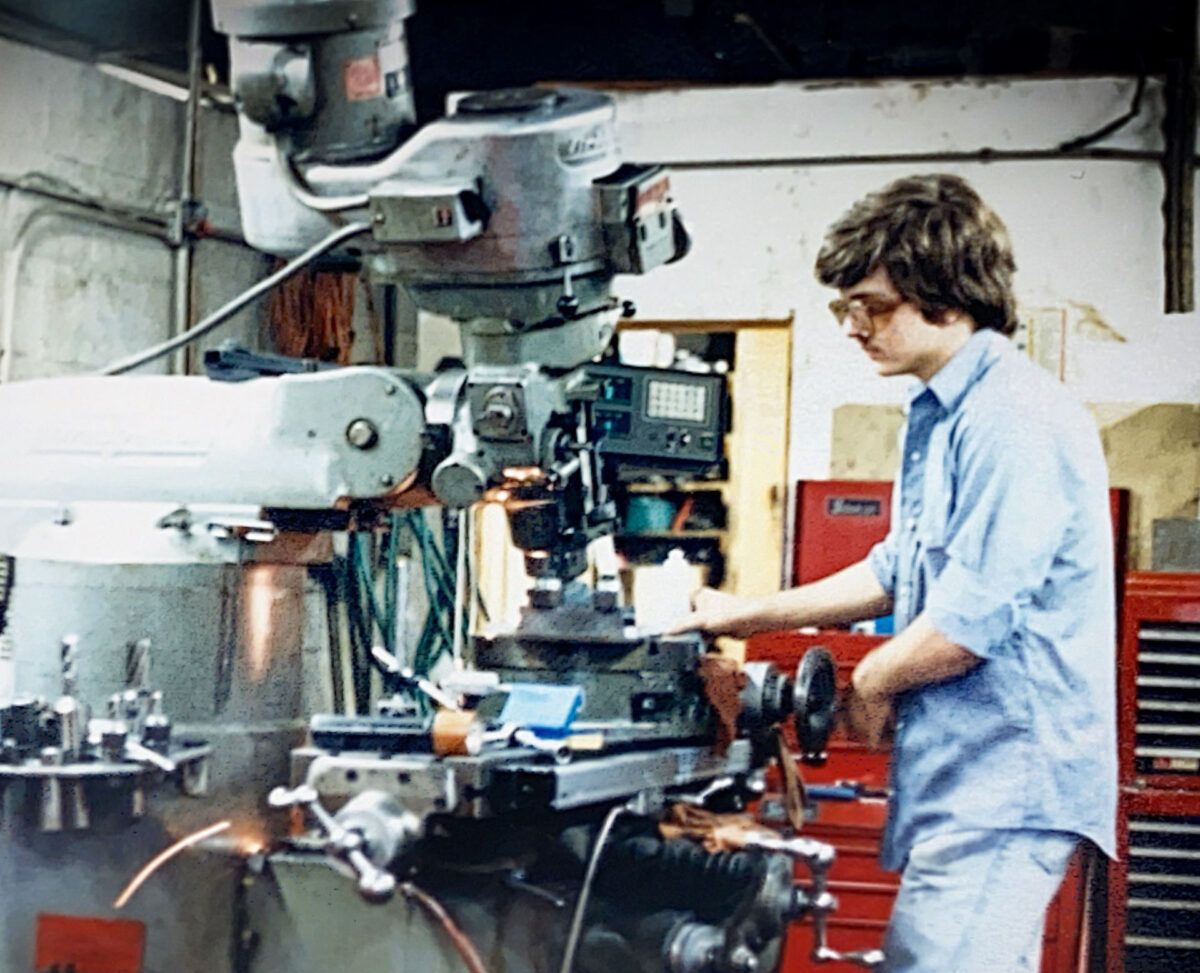
I think the benefit of that is we can achieve tolerances in parts and components today at a quality level that would have been unheard of for us to have achieved 10, 15, or 20 years ago.
Q: You’re well known for your barrels…how did it come to be that you began with barrels instead of pursuing complete ARs?
Bob Faxon, Faxon Firearms – When we decided to have a gun company, we didn’t want to have a generic business making barrels or AR-15s. We realized the competition was so stiff that we would not try to enter into it. I went out to Las Vegas for my first SHOT Show about 13 years ago, and my idea was that Faxon would make ARs because everyone else was doing it, and we had a machine shop that was not that busy. When I got out there, I saw how large the show was, and how many qualified AR-15 manufacturers there were. I came back and decided not to even try.
About six months later, my two boys and I were watching a Discovery Channel show about the top ten battle rifles of all time. The AK was number one, and the AR was number two. It upset me tremendously, and I went over to my kitchen table with a pen and grid paper, and on three or four pieces of paper I drew up our ARAK-21.
Being that it was an upper receiver that could fit on an AR lower receiver, the challenge now was to build it. We started on it, and along the way, we decided we would make our own barrels. We had been doing deep hole drilling for almost 30 years at that point. So, we started making barrels for the ARAK-21. Unfortunately, with internal testing, we found that we were not doing a very good job.
Q: What was the issue that you were having?
Bob Faxon, Faxon Firearms – We couldn’t get consistent accuracy. So, we had someone from the outside come in and help us. Our machining capabilities were never in question, but the nuances, the “black art.” or technique of making a barrel, had some requirements we were not aware of.
To help, we reached out to an outside expert. With some help from that gentleman, we found what we were missing…One of the things that we found that is so critical in making a high-quality product, especially in our pencil barrels, is the stress-relieving, post button-rifling. We had previously outsourced the stress-relieving process, but doing that was not giving us the final result that we needed.
We ended up coming up with a stress-relieving process that we believe is highly effective, and we took that process in-house. Today, we do all of it in-house, and I know it is one of the key factors for making a very, very high-quality barrel. Then you get into the finish machining, the chambering, the polishing of the chambers that we do.
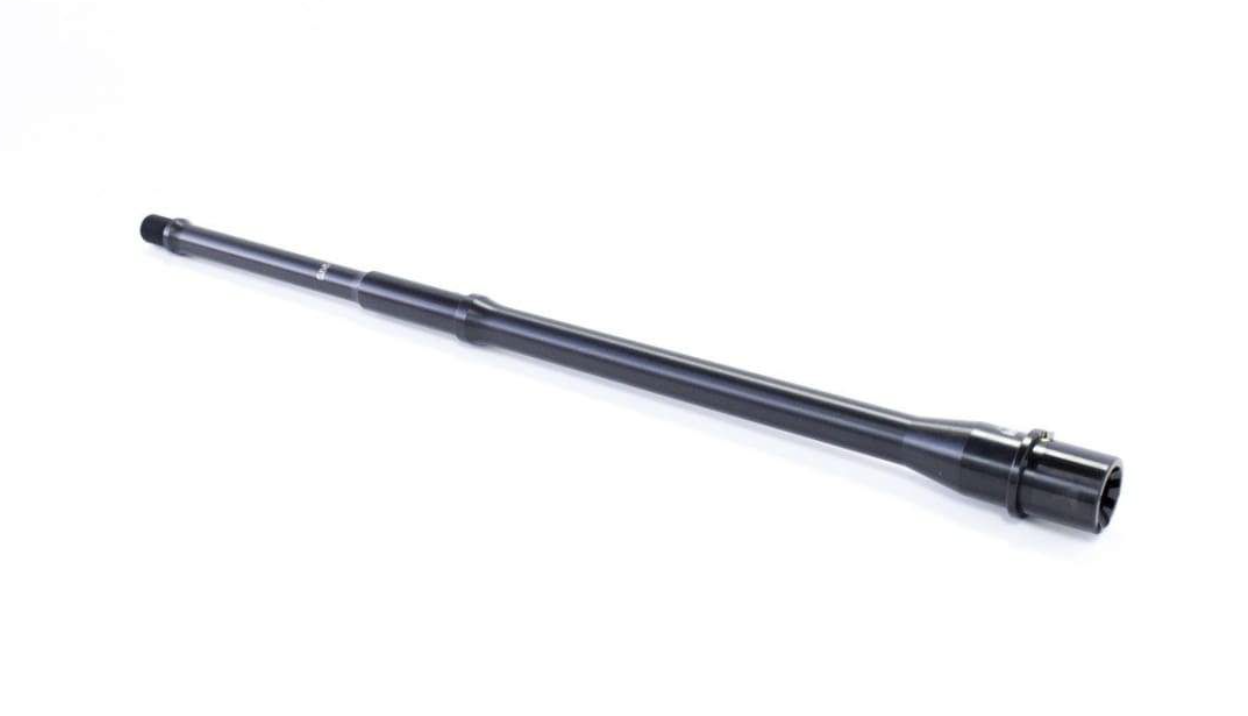
Faxon Firearms 16″ GUNNER 5.56 NATO Mid-Length 4150 Nitride
I’m very proud of the barrels we put out for the AR platform. We’re looking to make a high quality/value proposition in a barrel. As such, it’s always going to be worth it for us to add a few more seconds to make that barrel better better. Nothing we create at Faxon has a high volume “crank it out the door” mentality. I think there is a nice combination of hand work and TLC that goes into our barrels that makes them a little bit better.
And in addition to that care and attention, at this point we have over 40 years of manufacturing background. We were not a company with an idea that then had to learn about machining. Rather, we were a machining company that just had to learn about guns. I think it has worked out very well.
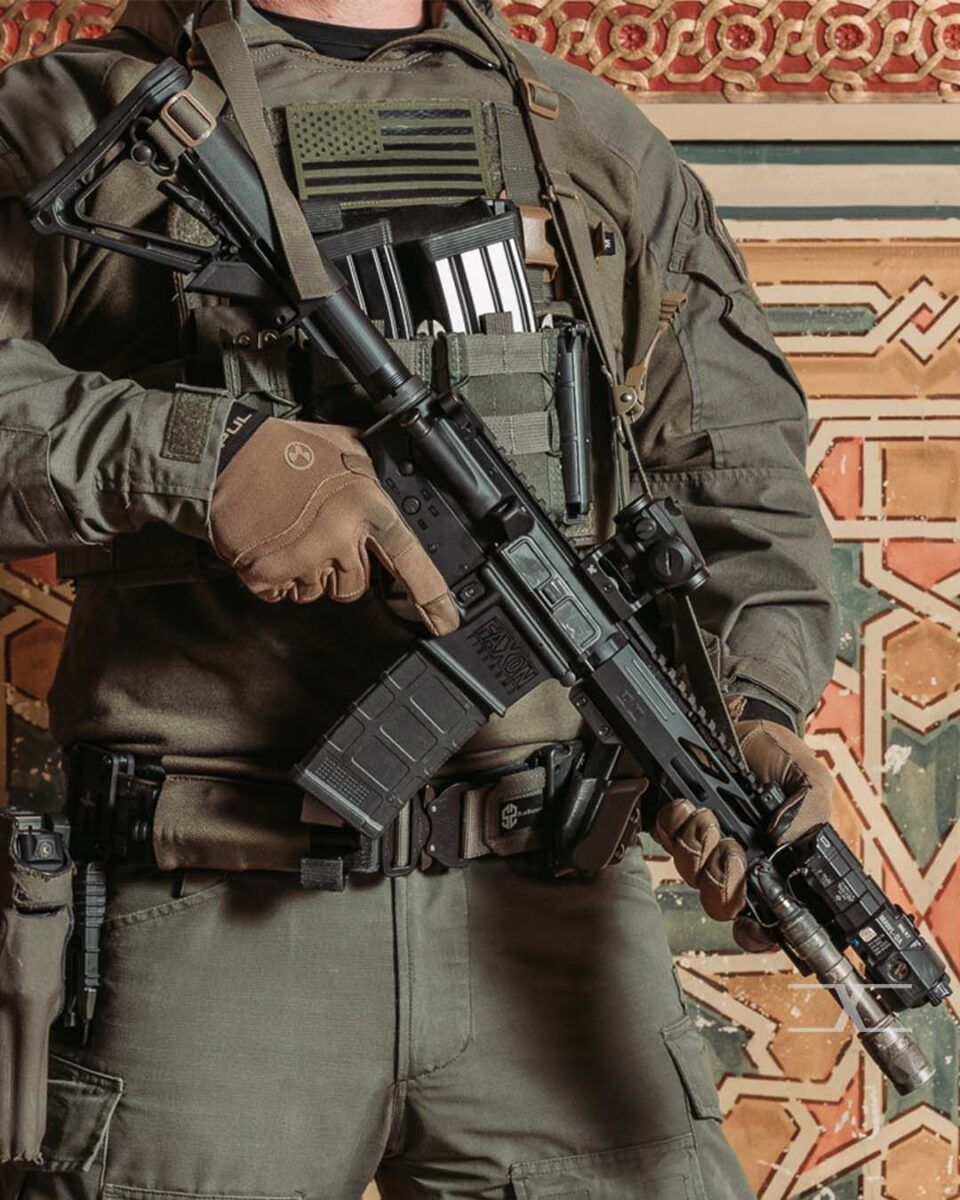
Q: I can recall discussions when the WWSD rifle came out about your pencil barrel, and how something like that wouldn’t have been possible years ago. Can you talk about that?
Bob Faxon, Faxon Firearms – I think the pencil barrel is a very straightforward engineering challenge. There are pressure issues that minimum wall thicknesses need to be able to withstand. You can’t defy physics, and there is a safety factor to consider. The bigger challenge with a pencil barrel is that if you heat the barrel up, will you get an increase in group size or will it string across the target?
If you look at the results of our barrels that a lot of people have done testing on, the typical results are that the group will open up, just like any other barrel because of physics, but it won’t string across the target. Again, that goes back to the stress-relieving process that we developed for all of our barrels. I think the sensitivity of our stress-relieving method impacts us not having the rounds string across the target as the barrel heats up.
Q: I have one of your flame-fluted 16″ barrels in a build that I love, and it’s been incredibly accurate, reliable, and the build is just fantastic to shoot. Can you talk a bit about that barrel? It reminds me a bit of the pitted barrels I see from Marvin Pitts at Nefarious Arms.
Bob Faxon, Faxon Firearms – There was a patent on the dimpled barrels, and we were not allowed to do those, so out of frustration, we asked what would be different than dimpling. Of course, straight fluting we had done, but we were out on the floor with some engineers, and we started playing with some things. We ended up coming up with and patenting our flame flute design.
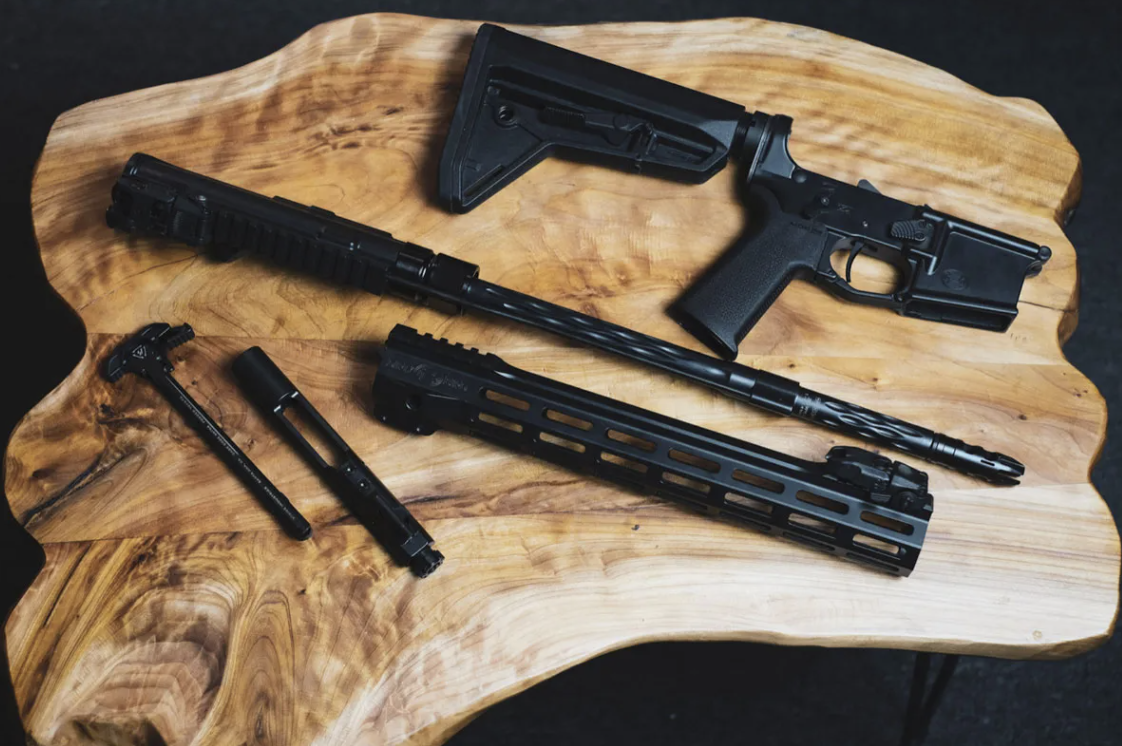
To be honest with you, fluting has a few primary purposes. Weight is one, and heat dissipation over the surface area is another. Is our flame-fluted barrel done for those reasons? Yes, it is, but it’s also obviously because it looks cool.
It also has one benefit over a straight fluted barrel. A straight fluted barrel will have a consistent minimum wall thickness at the root of the flute to all the way down the barrel. This is totally fine. However, if you look at the flame fluted barrel, it only has one very small area that is the minimum wall thickness. It then starts to gradually get thicker as it changes diameter radially as it goes down the length of the barrel. You don’t have a long strip of thin wall; rather, you have an oscillation that goes in and out.
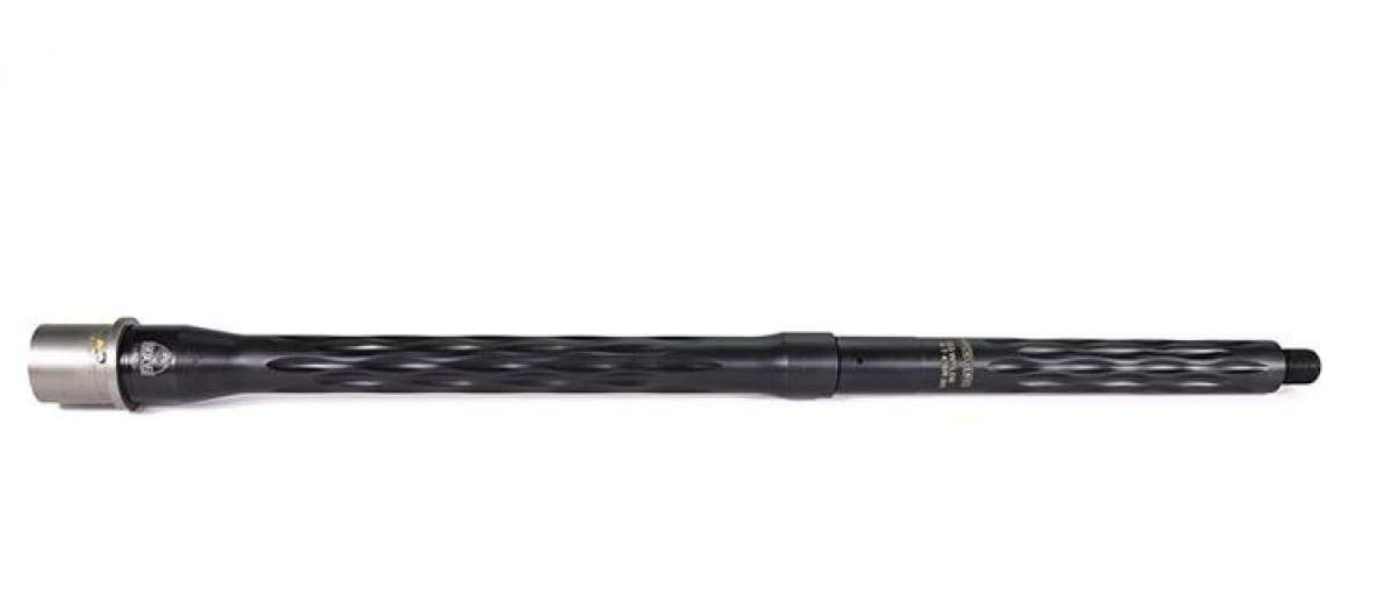
Faxon Firearms Match Series 16″ FLAME Fluted .223 Wylde
It’s a high-quality barrel. It’s manufactured the same way we make our other barrels. It is stress-relieved the same way. It has the same TLC in the manufacturing with consistent processes and a rigorous inspection, but it just has a different look. One of the things that our company really focuses on is that we want our customer’s experience to be positive. There’s a quality/value proposition. We don’t want to be the cheapest, nor do we want to be the most expensive. Our hope is we want you to come back from the range confident you got equal or better quality for the price you paid.
We also want to make sure our products are things that the customer actually wants. So, if the cosmetic appearance of the flame-fluted barrel is desirable to the AR builder, then that’s fantastic. We want to give them the option to own something a little unique and desireable.
Q: You offer barrels with built-in muzzle breaks and flash hiders. Can you talk about how that came about?
Bob Faxon, Faxon Firearms – I’m glad you asked that. We started making pencil barrels because people really liked them. We made pencil barrels, then we made the Gunner barrel. The beauty of Faxon is that we don’t mind reprogramming a machine tool if it is going to make a better experience for our customer.
While people really like our pencil barrels, they were putting a very light barrel into the gun, only to put a large brake on the end of it.
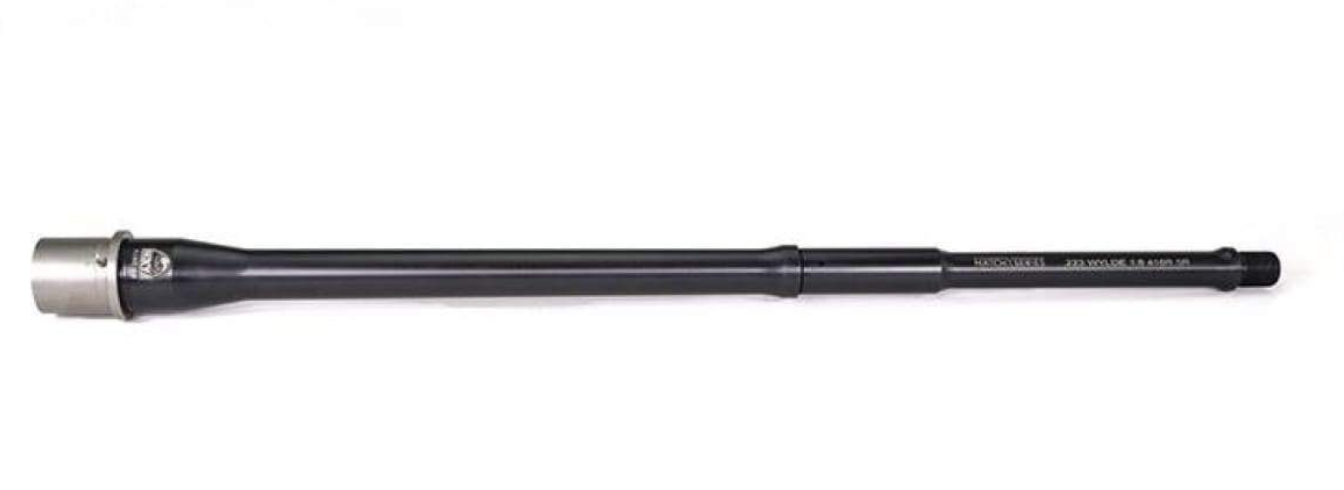
Faxon Firearms Match Series 16″ PENCIL .223 Wylde Mid-Length 416-R Stainless Nitride / Melonite 5R Nickel Teflon Extension Barrel
It looked like a big baseball sticking out there. It was a bit disappointing, and I wanted to do something a bit more low profile. At first, I thought that we should make a slim brake to match the barrel.
We started making these small muzzle devices, but when people wanted to then weld those muzzle devices on a thin-walled 14.5″ pencil barrel to get to 16″, it didn’t seem like a good idea even though, it was very carefully done. So, it was then that we decided to make everything one piece. This decision did introduce some engineering challenges regarding timing, etc., but the barrels have been a great success for us, and the feedback we get is tremendous.
Q: You’ve been putting out Glock products, as of late. Can you talk a bit about the idea to move into the Glock market?
Bob Faxon, Faxon Firearms – It was a natural evolution as we started filling out some of the SKUs that we wanted to build for the AR platform and barrels. We started making Glock barrels, and we found that we were pretty good at it. Of course, it was our kind of machining.
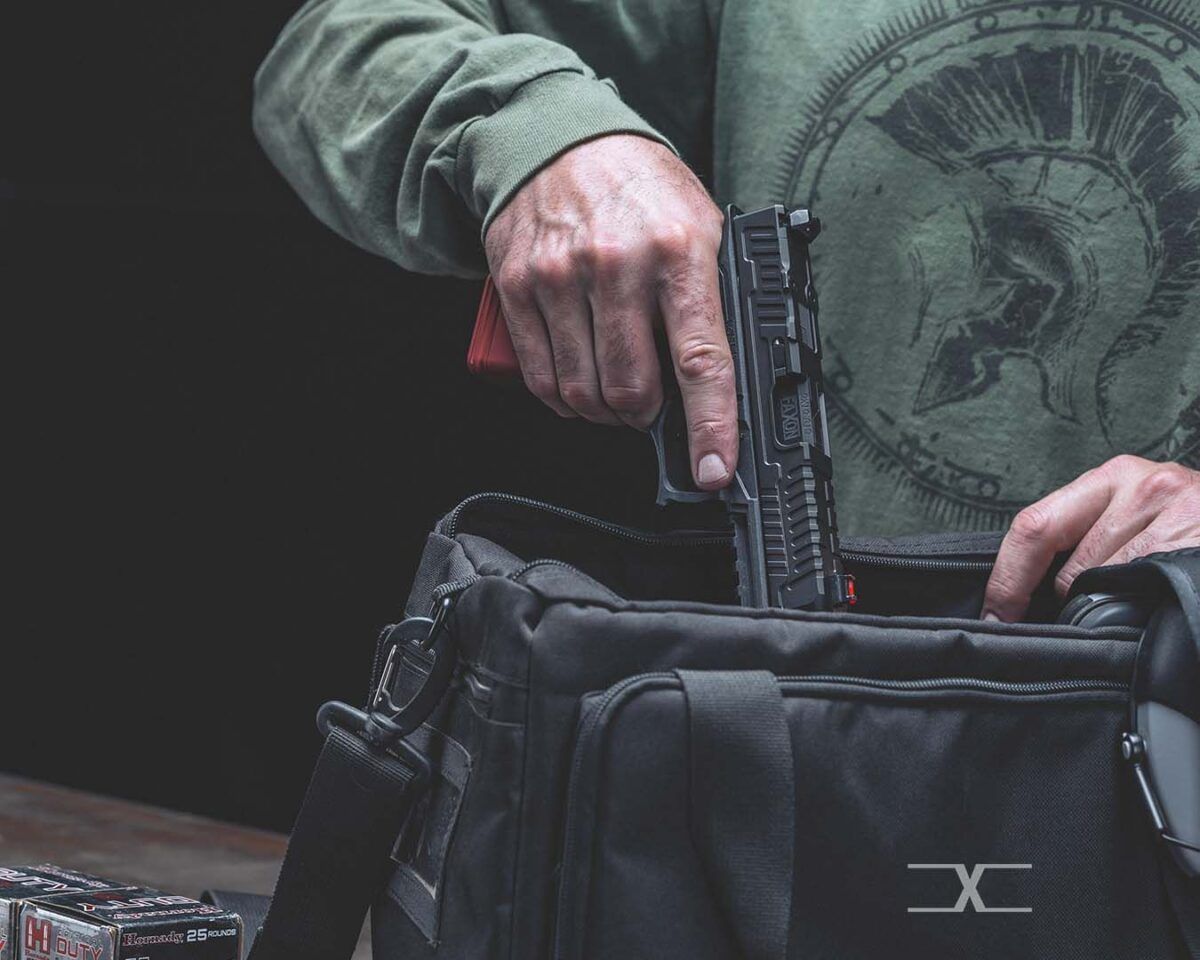
Once we started making slides, it started to make a sense to offer both our barrels and our slides together. We then thought “why not just put everything we do together in a complete gun.” It was very similar to the way that our AR pistols came about that we have today. It was simply because we had the handguards, uppers, lowers, barrels. Why not put it together in a gun?
While many of our customers are builders who like putting things together themselves, others want to buy everything together. I can understand that perspective, and I think it’s important to address that customer who does not want to build their own rifle or pistol.
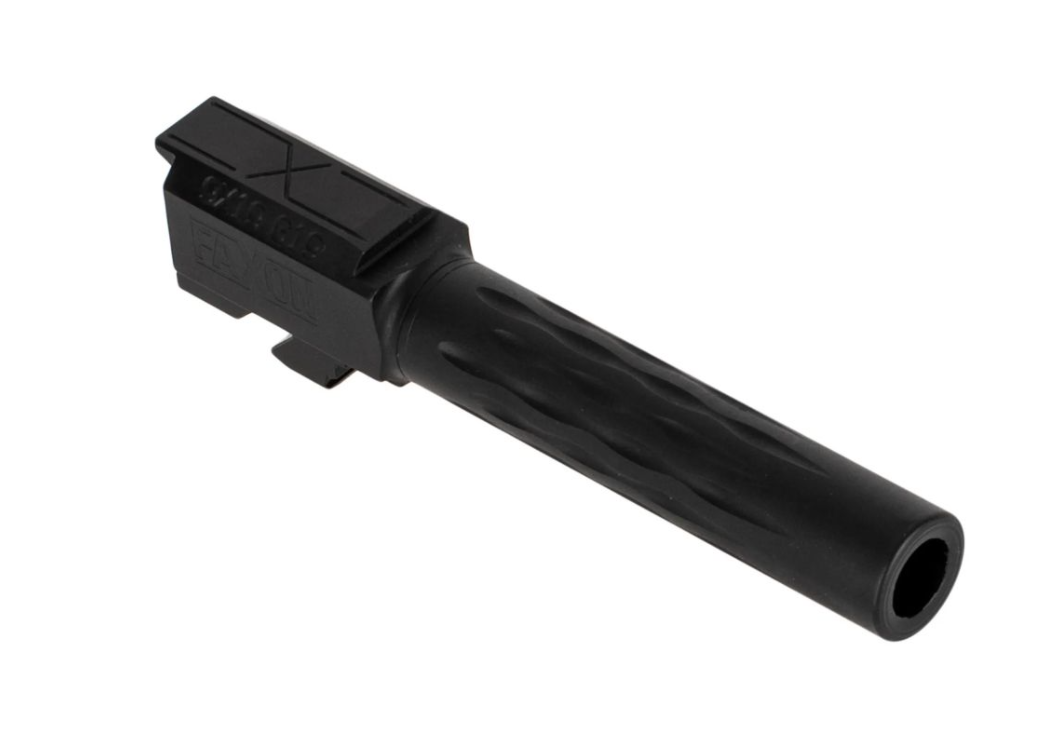
Faxon Firearms Flame Fluted Glock 19 Match Barrel – Non-Threaded
With our pistols, what we offer is a gun that is set up the way you’d want it after you bought a standard Glock. For instance, our Hellfire and Patriot pistols are red-dot ready machining with a cover plate. They have improved triggers, and more serrations for more aggressive, tactical-type shooting. In addition, you have a flared mag well on the Hellfire and a threaded muzzle for a suppressor or muzzle device.
They’re the modifications that we would personally like, and that’s why we offer them the way we do. The Patriot is a little more docile without the windows cut in the slide, without the mag well, and without raised sights for the suppressor…and the Hellfire is a little more aggressive.
Q: Finally, let’s talk about your involvement with 8.6 Blackout. What can you tell us about your 1:3 twist barrels that appear to be on the near horizon?
Bob Faxon, Faxon Firearms – One thing that’s unique about the 8.6 Blackout is it’s barrel twist. It’s a super high rate of twist at 1:3, and that brings about its own set of challenges. It’s a different process and a different question than the typical 1:7, 1:8, or 1:9 twist. When Q talked with Faxon, they spurred our team’s curiosity and our team banded together.
I can tell you it did not come easily. It was not as simple as someone who comes to us and says “hey, make me a 5.56 barrel with a new profile.” That’s not a problem. But with a new round and such a fast rate of twist, there are some manufacturing challenges that arise. It took quite a while to resolve some of those. Right now, the final outcome is that shooting the 8.6 Blackout, the accuracy they are achieving, and the actual benefit of the round is phenomenal.
Our 8.6 Blackout barrels are extremely good for reliability and accuracy. The nature of the round adds a lot of benefit by itself, but it if the barrel is not correct, that is an issue. It takes both. Through the development phase and where we are now currently, we have an incredibly positive set between the barrel and the round. For certain people, this is going to be very desirable. My guess is that when you see the ballistics and the results it produces, this round is here to stay. This is a good round and it’s going to stick.
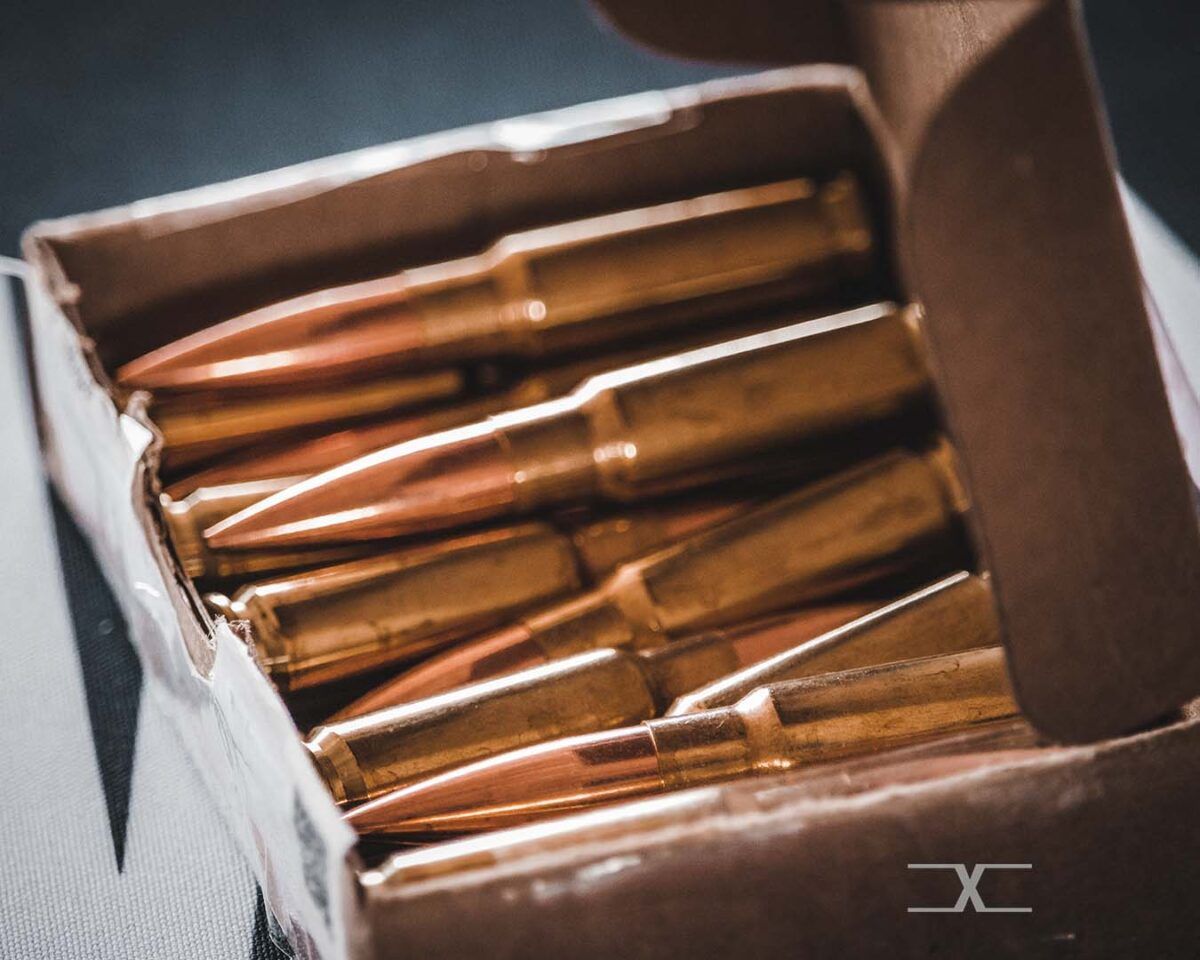
Q: Would you be willing to explain any of the specific manufacturing challenges you encountered in making a fast twist 1:3 barrel?
Bob Faxon, Faxon Firearms – I would say that is something that we’d prefer to keep under wraps because it took quite a while to get it right. The process took quite a while to develop, and its quite a bit more challenging than a more standard twist rate. It took a lot of creativity and innovation. It certainly wasn’t your standard “buy a machine, buy a button, make a barrel” situation.
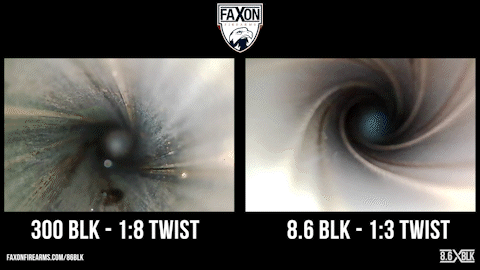
It was much more challenging, but I would also say that the capability of us making that barrel at Faxon Firearms is extremely high right now. We are producing extremely high quality and incredibly consistent barrels in 8.6 Blackout. It’s not like you get one out of 10, or you have these problems where you get one good one and one bad barrel. It’s nothing like that.You have to have a robust process. When you manufacture things, you can’t be pulling a rabbit out of a hat, and it can’t be the best guy producing on his best day. I would say that Faxon Firearms has developed a very robust means and way to produce 8.6 barrels in a cost-effective manner.
Q: I’d imagine working with Q on the 8.6 project at such a high level has got to be an exciting accomplishment for your company….
I do think it was an exciting and noteworthy accomplishment. Our team worked very hard to achieve what they have in manufacturing the 8.6 barrel, but I would say that is not a totally unique experience for us.
You have to remember, our other manufacturing business has been doing these types of challenges for many, many different customers for many years. So, the challenge that Q presented to Faxon Firearms was not unlike other challenges that we have resolved. We’ve got products on the ocean floor and on Mars.
That said, our 8.6 Blackout barrels are certainly a big win. It’s a high technical achievement for a very important product. The 8.6 Blackout is a fantastic round, and I want to promote it. It’s going to stay around, and people are going to want it. It does feel good though. When you win, and you produce something really good, and it works great, it’s very satisfying, especially when it takes a little bit of work to get there.
###
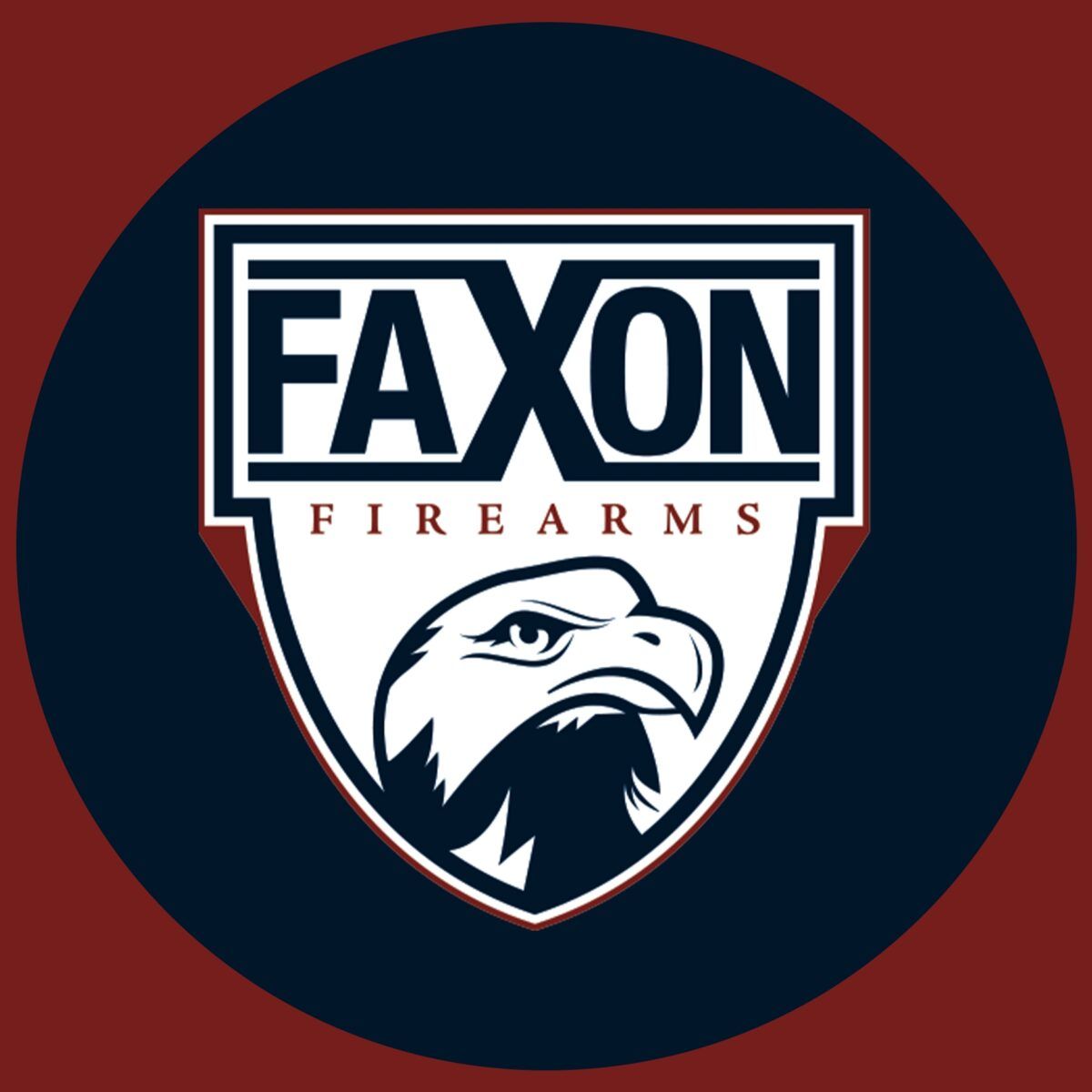